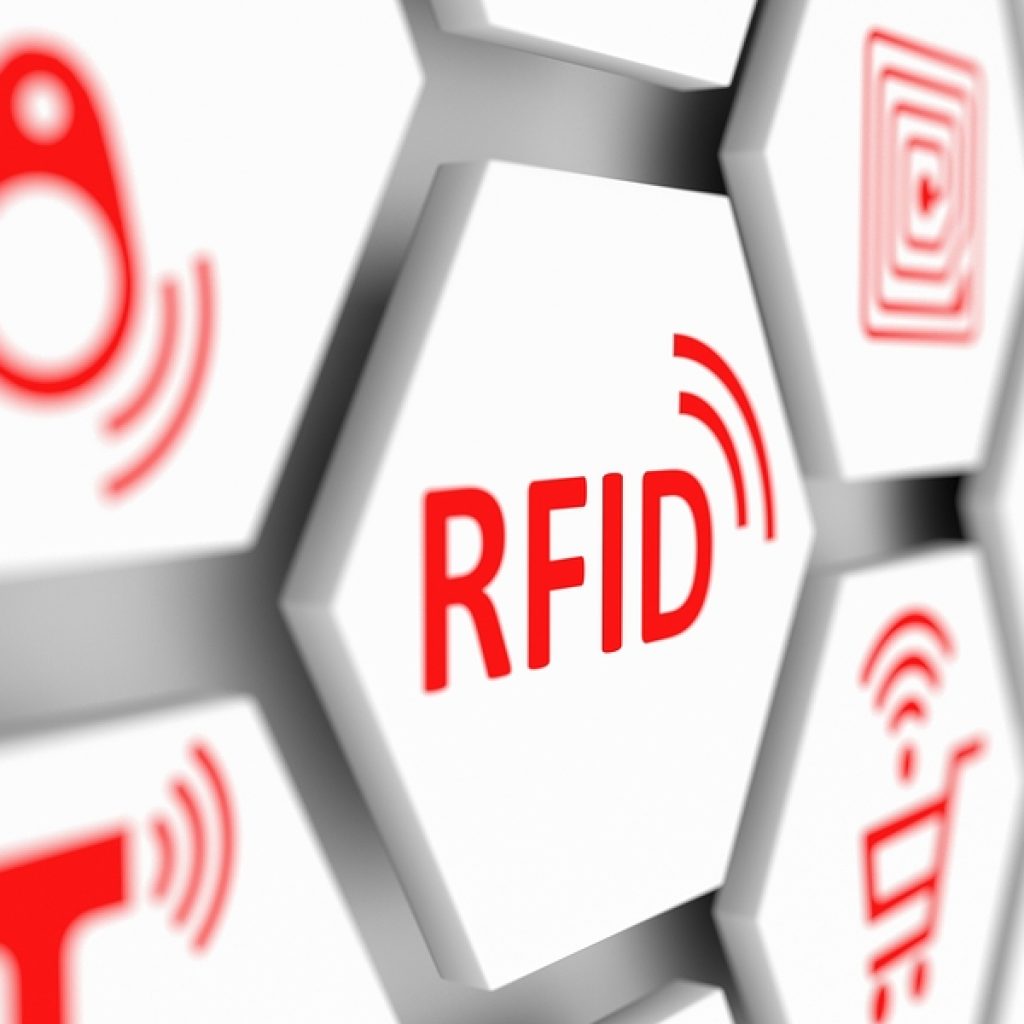
If you are new to the RFID world, no doubt, you have a lot of questions. RFID Inlay and tags can be a bit confusing. However, we are here to lay it all out for you so you can figure out the best course of action for your labeling process.
This article covers RFID inlay, tags, RFID readers and how they work, and common challenges.
Related: What is RFID? Basic Terms and FAQ
Related: What You Need to Know to Create the Best RFID Label Solution
PaladinID has been helping companies like yours for decades with labeling and printing solutions that save time and money. We can help you figure how to incorporate RFID into your existing system or create the perfect new one.
Call PaladinID today to find out exactly what you need to “Make Your Mark!”
Please give us a call at (888) 972 – 5234 or email us at info@PaladinID.com.
What is an RFID inlay?
Functionally, an inlay consists of an antenna and a microchip. The antenna drives tag performance and governs how well the tag will work in a particular application. Precision-designed to receive and broadcast RF signals, the antenna is made from a conductive material (such as silver, copper or aluminum). The antenna makes contact with an RF reader over a distance determined in large part by the amount of metal and size of the antenna.
Contacts attached to the microchip make the circuit between the microchip and antenna. The chip design determines the protocol or class of the tag’s operation. Different microchips have different features that can also affect performance. RFID microchips contain circuitry capable of handling a variety of functions from power conversion to data storage and retrieval.
What are RFID inlay antennas made of?
Traditionally, RFID antennas were etched from copper — a relatively slow, relatively wasteful process. Today’s antennas tend to be produced with more efficient methods such as etching or stamping. What does an RFID strap consist of?
A strap consists of a microchip with two oversized contact pads on a carrier sheet to facilitate high-speed roll-to-roll manufacturing. In conventional flip-chip manufacturing, the microchip is a very small component, less than 1mm square with tiny contact pads that must be placed very precisely on the antenna. This is a relatively slow process. To overcome this problem, Avery Dennison RFID Division has developed an innovative high-speed strap attach process that substantially improves yield rates.
Are there different versions of inlay?
Yes, there are three main versions that are typically used:
- Dry Inlays – a polyethylene terephthalate (PET) substrate with an RFID chip and antenna bonded to it and then sandwiched with another protective PET lamination layer and delivered in roll form.
- Wet Inlays – a Pressure Sensitive Inlays – same as Dry Inlay above, with the addition of a “wet” adhesive backing and liner.
- Encapsulated or Durable Finished Transponders – an inlay with the addition of a durable encapsulate for longer tag life.
What is an RFID tag?
An RFID tag is a label that has an RFID inlay inserted between the label facestock and liner.
What is the difference between active, semi-passive and passive tags?
Active tags broadcast under their own power, using an onboard battery. As a result, they can have very long read ranges. They are more expensive than passive tags, so they’re normally used to tag very high-value items.
Passive tags are the most economical RFID tags and the most common tag used in supply chain applications.
They don’t have onboard batteries like active tags, because they get their power from RFID readers. The RFID reader sends electromagnetic waves to the tag’s antenna. Using energy from these waves, tags broadcast a signal back to the reader.
Semi-passive tags are a small and light-weight hybrid of active and passive tags. They generally use a battery to power the electronic logic (like active tags), but can also transmit data using power generated from RFID readers (like passive tags).
What are the components of an RFID tag?
An RFID tag has a protective/printable facestock, then a layer of adhesive, then the RFID inlay, then another layer of adhesive, and finally a removable liner. The RF inlay provides the RFID functionality. The inlay consists of a carrier sheet that holds an RF antenna, to which is bonded a tiny microchip. The liner and facestock are typically made of paper, but may also be made from other materials such as plastic films. The selection of materials determines how well the tag will survive and whether it will be compatible with printers, applicators and
other system hardware. Material selection may also have to accommodate FDA regulations. In addition, there are mechanical considerations, such as selecting an adhesive that will ensure the tag will remain adhered to the carton.
What frequency does RFID run on?
Like all wireless communications devices, RFID tags and readers operate under assigned frequencies. In the United States, these frequencies are assigned by the Federal Communications Commission (FCC). The European Union’s frequency assignments are governed by the European Telecommunications Standards Institute (ETSI). Most of the world uses frequencies defined within the ETSI or FCC designations.
The FCC allows several frequency bands to be used for RFID including the 125kHz, 13.56MHz, and 902 to 928 MHz bands. Low Frequency (LF) tags operate in the 125kHz range. Tags operating in the 13.56 MHz range are referred to as high frequency (HF) tags. RFID tags operating 902 to 928 MHz band are referred to as ultra high frequency (UHF) tags. In North and South America, for example, 902-928 MHz band is commonly used for asset management. The ETSI recommended UHF RFID operational frequencies for Europe are between 865-868
MHz. While there are many differences between UHF and HF tags, the most relevant differences are the
following:
- UHF tags have longer ranges and are thus more suitable for supply chain applications (i.e. reading cartons and pallets at a distance of tens of feet).
- HF and LF tags have shorter ranges and have therefore been the technology of choice for proximity applications such as library book tagging and security access control (i.e. reading at a few feet).
Many applications like retail apparel tagging and supply chain applications are based on the 902-928 MHz frequency band. Applications for payment cards and library book tagging use the 13.56 MHz band.
What is an RFID reader?
RFID readers supply power to passive and semi-passive tags and communicate with them. For these reasons, they need to be installed at critical points throughout the supply chain. There are also handheld readers.
RFID readers typically include several elements:
- Digital signal processor and a microcontroller
- Internal or external antenna
- Network or serial port connection
- Input/output ports for linking to other devices
How does an RFID reader work?
Readers emit radio waves. The antenna within the RFID tag receives these waves and collects energy to power the microchip. If the reader signal is too weak, then the tags cannot collect enough energy to “wake up.”
How is an RFID tag encoded?
RFID tags can be encoded with a stand-alone reader/antenna setup. However, in a typical real-world application, that function is accomplished within an RFID-enabled printer or printer/applicator.
How is an RFID tag printed?
In an RFID implementation, the tag can be encoded, verified, printed and even applied to the box by one machine. The RF inlay adds a level of complexity to an otherwise fairly straightforward process. Both the microchip itself and the edges of the inlay cause “bumps” in the otherwise flat label surface. This can cause print distortion. Perhaps even more problematic, the RF environment inside each RFID printer is different. Printer and inlay manufacturers are hard at work within EPCglobal to develop standards to address this.
However, for now, the differences between the inner cavity of the printer and the reader antenna location often require unique inlay orientation and placement for labels used on different printers. Also, spacing between smaller labels often needs to be increased to prevent more than one tag from being programmed at the same time. Stand-alone printers can try more than once to program a tag. However, a printer/applicator must keep up with cartons moving along the conveyor and therefore must discard tags it cannot program the first time.
How is an RFID tag applied?
There are a number of options available for automatically dispensing and applying the tag. Factors that affect the selection of an applicator include label size, carton speed, carton placement, and height variation and placement accuracy requirements.
The preferred methods are semi-automated or automated “Print-and-Apply” processes. In these systems, cartons are fed to the label applicator by hand or preferably by conveyor. Another label printer at the end of the process prints a pallet level label that’s applied before the palletized load moves through the RFID portal.
Do the contents in a package or carton pose a problem for RFID?
A carton’s contents can alter tuning and interfere with the tag’s ability to receive energy from the reader. Certain substances, especially metals and liquids, can often have a dramatic effect on the RF performance of tags. For this reason, these materials are often called “difficult” or “RF-unfriendly.” Aside from de-tuning, these materials can cause other problems like absorption, shielding and reflections.
How does the inlay orientation to a reader or position on a carton pose a challenge?
Many inlays, especially those with a small vertical profile, have an antenna read field pattern that resembles a donut, meaning that they cannot be read from the direction of the antenna tips. This can cause null spots (no reads) when trying to read the tag end-on. That is why Avery Dennison RFID designed our AD-831 inlay to be read from any orientation, with no null spots allowing it to be read from any direction.
Carton contents can also influence read range and there are many examples of a tag that reads well in one place on a carton and not at all when moved a few inches. Carton contents and their arrangement inside the carton can create hot spots and dead spots on the cardboard surface. Avery Dennison developed our Sweet Spot tester to determine the optimal RFID tag position on a carton relative to the contents inside.
How does read range pose a challenge?
As tagged cartons and pallets move through the supply chain, they interact with readers mounted in a variety of locations. They must be able to reliably broadcast all the way back to each reader. However, tags offering too much read range can cause serious operational problems if they’re seen by the wrong reader. Far-field performance rates how well a tag is read over the distance to the reader. Near-field performance rates how well the tag performs in an encoder/printer/applicator, where the reader antenna is only inches away from the tag at most. These performance rates must be balanced to tune tags to be read well both near and far.
How does the size of an inlay pose a challenge?
In RFID applications, size and form factor matter. Generally speaking, all other things being equal, the larger the tag antenna, the more cross section it has to receive and broadcast signals so the “better” it performs. That said, bigger antennas cost more and they may be over-engineered for a given application. Package space limitations also impose parameters on tag size. The inlay’s form factor, or size, must also match the type of insertion equipment used in the label converting process, as well as the physical specifications and capabilities of the
RFID encoders/printers/applicators being utilized.
How does the environment pose a challenge?
An RFID label is a fairly sophisticated communications device. It contains a microchip which could be subject to physical damage, data corruption and damage from electrostatic discharge (or ESD). An RFID tag is also a pressure-sensitive label subject to the same environmental challenges as any self-adhesive label, including physical impact, abrasion, moisture and excessive temperatures.
Why are quality and testing important?
RFID testing provides necessary data on both component quality and expected performance in real-world conditions. Avery Dennison RFID employs an “end-to-end” testing approach, challenging the quality of our inlays from prototype to delivery. Our Atlanta Technical Center simulates the real-world of the supply chain with conveyor, portal and RFID printer and printer/applicator hardware.
What is component testing?
Component testing assures that the inlay’s electronic portions will perform as expected. Different test protocols must be followed for different classes of microchips to evaluate near-field performance. This testing protocol includes a “writing to chip” test performed on Class 0+ and Class 1 inlays (including Gen 2). Another component of the testing protocol is the read sensitivity test. This is performed on all inlays to make sure they meet far-field requirements.
What is “free space” testing?
Tests performed in free space (i.e. performance tests of unattached tags conducted in a controlled environment) are the starting point for performance tests. Although these tests provide good baseline information, they provide insufficient information on which to select tags for specific applications. Carton contents, the orientation of the tag toward the reader antenna, and other environmental issues such as radio frequency noise and physical object interference can impact performance.
The Wrap Up in RFID Tags and Inlays
We hope this has answered most of your questions about RFID tags and inlays. As you can see, there are a lot of components and things to consider. Luckily, we have walked many companies just like yours through the process of creation the perfect solution that fits your exact needs. To learn more about RFID Ecosystems check out my interview with Michael Shabet, an industry leader in enterprise RFID ecosystems.
If this is your first RFID application it is best to bring in an experienced Systems Integrator to help layout the framework for the project and offer guidelines on what type of solutions should be considered.
Call PaladinID today to find out exactly what you need to “Make Your Mark!”
Please give us a call at (888) 972 – 5234 or email us at info@PaladinID.com.
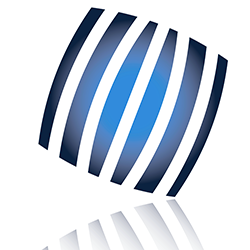
Got Labeling Questions? Our AI Assistant Has Answers - Chat Now!
For more information on PaladinID
Get Help With Your Next Label Project
We have over 35 years of providing exceptional service and labeling products to the world. Take the first step to an easy, stress-free solution for your label needs by contacting us.
Schedule a call below or email dritchie@paladinid.com
Make Your Mark
“Making companies more competitive by offering the correct label printing solution, on time, within budget, while creating unmatched value”.
About PaladinID, LLC
PaladinID develops and supports high-performance barcode labeling applications. We work with our clients to “Make Your Mark” by providing the expertise and tools necessary to create an entire product label printing solution. Located in central New Hampshire, PaladinID has been serving Massachusetts, Vermont, Maine, Connecticut, Rhode Island, New England, and beyond for over 30 years, and in 2017, became an RFID-certified company. We look forward to working with you.
You may be interested in our other services:
Product Labels
Product Labels
Labels for every type of application: Blank, Pre-printed, Variable data
Label Printers
Label Printers
We sell and support: Direct/thermal transfer, Inkjet, Laser
Printer Ribbons
Printer Ribbons
We sell ribbons for ALL barcode printers including: Zebra, Datamax, Sato, Intermec
Flexible Packaging
Flexible Packaging
We offer a wide variety of packaging containers for your products.
Label Software
Label Software
Software for all barcode printing and product labeling.
Label applicators
Label Applicators
Wide selection of applicators: Desktop/Mobile, Applicator only, Print & apply