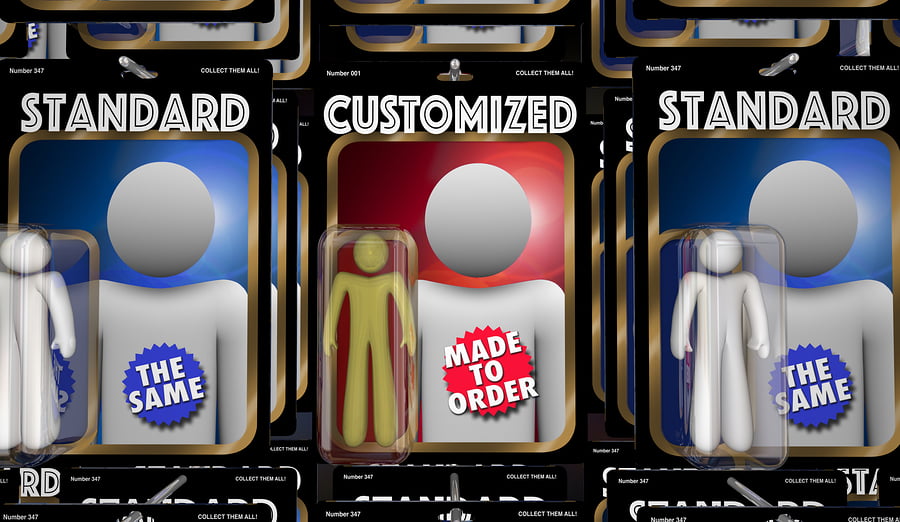
Simplifying Barcodes by Connecting Inventory Logic with Custom Order Specs — Custom (or Make-to Order) manufacturers, sometimes called “Jobbers”, typically produce a wide variety of products with different dimensions, colors, sizes and other features. We can connect the commonalities in these variations with “license-plate” tracking barcodes to an item or a container, such as a box or pallet, of items. Then we associate the tracking barcode with the part number for the item or items within the container and record the quantity in the container and its location Here’s an example:
Barcode Tracking Issues
A T-Shirt printer buys models of blank T-shirts. Each model will come in a variety of sizes and colors, but they have only one model number. When the T-shirt printer receives a customer order for a mix of sizes and colors with a customer’s graphic design, printed onto the T shirt. In implementing a barcode tracking system, we need to ask:
Q: What part numbers should be used to track inventory?
One Answer could be: Our manufacturer of T-Shirts assigns a separate part number to every size and color of every model of T-shirt to use as their raw material. This quickly leads to an explosion of part numbers that becomes a tracking nightmare.
OR
The manufacturer could use a single part number to track each model of T-shirt and then assign subsets for specific attributes, such as size and color of every T-shirt in stock. This reduces the setup data to one part number for each model. At time of receipt, T-shirts with the same part number but different attributes can be tracked to different barcoded bins, as they are received.
A similar approach is used for finished goods, where a separate, finished goods part number is assigned to each model of T-shirt. Here the attributes, captured at the time of order, will not only be the color and size of the T-shirt but also a reference to the graphic design to appear on the T-shirt. By using the same subset logic, only a single part number, corresponding to the T-shirt model, is entered for each sales order line, along with the attributes the customer wants.
An inventory and work-in-process tracking system will automatically launch make-to order jobs from each sales order line. These jobs are for the finished goods part numbers but also inherit the attributes specified on the sales order line, such as size and color and model of T-shirt to be used as well as the graphic to be applied.
The Setup Process
The setup process can be simplified and designed to replicate by establishing templated routes, consisting of a sequence of processing operations associated with each job, or standard routes can be set up for each model of t-shirt which will be automatically associated with the job. These routes can then be easily modified for special operations, when needed for specific orders.
Using barcode scanning to record material in, out and returned, as well as any scrap that results. We also record the elapsed time for the operation and the amount of labor required. Thus satisfying external reporting requirements, such as order fulfillment as well as internal tracking of inventory.
Raw materials, such as blank T-Shirts, recorded into a job are tracked not only by part number but by attributes such as size and color. This is so that raw materials inventory can be tracked, not only by model of t-shirt, but by each size and color in stock, and where each is located in the stock room.
Similarly, attributes are used to track returned material and to warn users if they attempt to mix materials with different attributes, such as T-Shirts with different sizes, in the same barcoded bin. As with most make-to-order processes, T-shirts go through a sequence of operations, which result in T-shirts being in a variety of intermediate states. Using this inventory hierarchy, our manufacturer does not have to assign different part numbers for the T-shirts in each intermediate state (or even worse for each different model, size, color and intermediate state) in order to track the work-in-process inventory.
By tracking work-in-process (WIP) as the finished goods part number (and attributes) and then setting a WIP flag on the barcoded containers holding the WIP material, we can ensure that this inventory is not confused with finished goods inventory but is clearly identified with the part that is being made and the operation that was just completed.
The Benefits Include:
- Not creating part numbers for the intermediate WIP products, while maintaining real-time visibility of all the WIP materials for each job and customer order as they flow from operation to operation.
- Packaging finished products in barcoded containers. In our example, the finished T-shirts will typically be placed in plastic bags. The system can print out barcode labels on demand for each bag, with a unique tracking barcode and details of the product attributes such as T-shirt model size and color and the graphic image or logo applied.
- Associating the tracking barcode on the bag or other container with both the customer order AND the manufacturer’s inventory all in one database
- System generates barcoded picking sheet for the order, so that as each line item is picked and packed, the barcode for the line item is scanned along with the barcode on the bag or other container being picked.
Result = Accuracy:
By implementing ATTRIBUTE MATCHING, your system is recording the model number for the T-shirt, verifying that it is correct by cross-referencing the attributes such as size, color and logo and matching it to the sales order line and the items being picked. If the attributes do not match, then the person doing the picking and packing is immediately alerted that they are picking an item that does not match the required attributes from the order. This same attribute matching can be used on picking raw materials for a job where a picking sheet is generated for the raw materials needed for the job, Including the attributes such as model, size and color. When the bin barcode is scanned, from which raw materials will be withdrawn, after scanning the barcode on the picking sheet, the person doing the picking will be alerted if they have selected the wrong size or color material for a job.
Barcode tracking systems provide features to optimize item attributes to appear on sales order acknowledgements and packing slips, as well as on barcoded travelers for jobs and barcoded picking sheets. The system can also be programmed to enable the specification of order-specific instructions for making the products and the capture of user defined parameters (such as percentage complete) to be captured on job steps.
Commentary on Simplifying Barcodes
For many make-to-order manufacturers, the use of attributes can dramatically simplify the setup and capture of data in a barcode tracking system. It can also prevent many expensive mistakes and dramatically simplify the setup of item master records in accounting systems, and their corresponding account sets, by keeping the number of item master records to a minimum.
The is an excerpt from © BellHawk Systems Corporation blog: Barcode Tracking Simplified or Make-to-Order Manufacturers.
About Bell Hawk
BellHawk Systems provides its BellHawk real-time inventory and operations tracking software to manufacturers, distributors, food processors, laboratories, engineering and other industrial organizations. It also provides related professional services to assist its clients in implementing these systems as well as in integrating these tracking solutions with their ERP, CRM, accounting, E-Commerce and other systems.
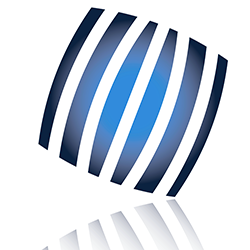
Got Labeling Questions? Our AI Assistant Has Answers - Chat Now!
For more information on PaladinID
Get Help With Your Next Label Project
We have over 35 years of providing exceptional service and labeling products to the world. Take the first step to an easy, stress-free solution for your label needs by contacting us.
Schedule a call below or email dritchie@paladinid.com
Make Your Mark
“Making companies more competitive by offering the correct label printing solution, on time, within budget, while creating unmatched value”.
About PaladinID, LLC
PaladinID develops and supports high-performance barcode labeling applications. We work with our clients to “Make Your Mark” by providing the expertise and tools necessary to create an entire product label printing solution. Located in central New Hampshire, PaladinID has been serving Massachusetts, Vermont, Maine, Connecticut, Rhode Island, New England, and beyond for over 30 years, and in 2017, became an RFID-certified company. We look forward to working with you.
You may be interested in our other services:
Product Labels
Product Labels
Labels for every type of application: Blank, Pre-printed, Variable data
Label Printers
Label Printers
We sell and support: Direct/thermal transfer, Inkjet, Laser
Printer Ribbons
Printer Ribbons
We sell ribbons for ALL barcode printers including: Zebra, Datamax, Sato, Intermec
Flexible Packaging
Flexible Packaging
We offer a wide variety of packaging containers for your products.
Label Software
Label Software
Software for all barcode printing and product labeling.
Label applicators
Label Applicators
Wide selection of applicators: Desktop/Mobile, Applicator only, Print & apply