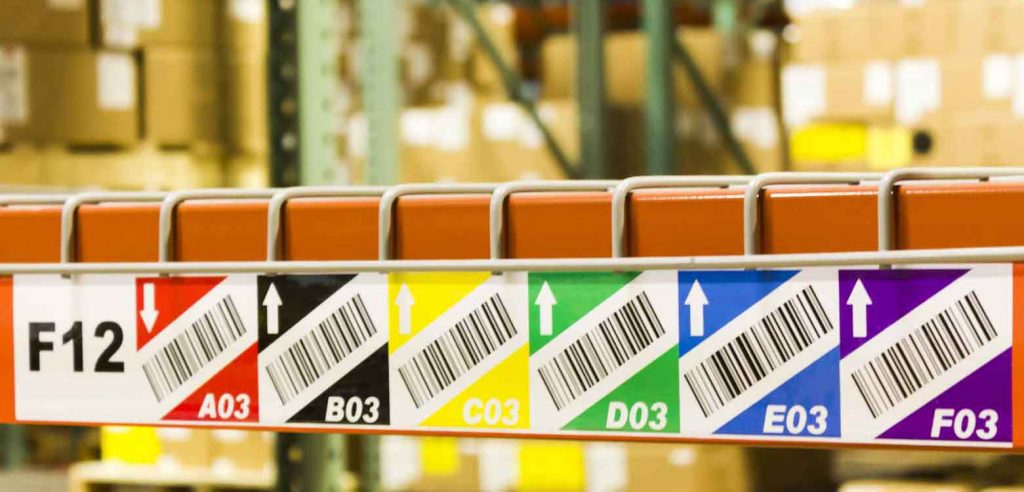
In this day and age of big-box and warehouse stores, most of us have walked through a warehouse…whether it’s wandering through a BJ’s or Costco, or searching for a furniture SKU in IKEA. Retail stores certainly face some challenging label problems. With the advent of barcodes and far-field (distance) scanning, using barcode technology to organize and locate warehouse inventory is something that we all probably take for granted, and almost certainly we rarely pay attention to the labels on those orange and green steel racks.
Warehouse labels enable manual and electronic product location and picking. These barcode labels are often color coded, and reflective to help make identification and location easier in dark corners. Labels also can be made removable, so that they are easy to relocate, since inventory and storage configurations are constantly changing. Warehouse labels are the physical tags that support a warehouse’s organization system, creating flags on the floor that are linked to an inventory map. Barcodes are used to connect product information to items, barcode labels enable warehouse personnel to track physical inventory and manage items efficiently so that the inventory can be received, picked and shipped with minimum duplication of efforts.
A Warehouse Labeling Case Study – StripeItRight.com:
Solving Challenging Label Problems
One Tuesday a few weeks ago, I received an urgent call from Brian, owner of Stripe It Right. His company stripes commercial parking lots and warehouses along with various other marking solutions. He was in the last stages of completing a warehouse buildout for a national retailer, with a commitment to turn over the facility the following Monday. One of the last project tasks was applying barcode labels on all the racks in the warehouse. Brian had found PaladinID doing a Google search on warehouse labeling. He was in a bit of a jam because his label supplier was not able to produce and deliver the labels that Stripe It Right had ordered a month before.
Stripe It Right needed warehouse rack barcode labels and they needed them ASAP! I assured him that PaladinID supplied these types of barcode labels and we quickly got to work identifying the project needs. The solution was retro-reflective and white labels with pre-printed barcodes as well as rack location ID labels. I recommended using a polyester label for both applications with a lamination to protect and preserve the preprinted barcodes and data. This additional protective coat keeps the label legible and scannable, even if brushed or bumped by a forklift, pallet or warehouse ladder.
Stripe It Right needed labels by Friday at the latest because weekend crews were scheduled to install the rack labels throughout the entire warehouse. I told him I would get right on his project and rally the troops to see if we could pull this off. The timeline was tough, and I committed to putting PaladinID’s best efforts on this project to try to make it happen. There were lots of obstacles, but our extensive resources made me feel that we could pull this off, if all the stars were aligned! Brian and I hung up with a clear course of action, and I got to work.
First, I contacted our plant manager and put together a plan. We determined that If the plant had the label order by Tuesday afternoon, they could ship labels out on Thursday. Overnight delivery would put them in Brian’s hands on Friday – just before the weekend. Brian was thrilled! By Thursday the labels were ready for shipment. Brian received the labels Friday afternoon and started his crews labeling every rack in the warehouse. They finished over the weekend with time to spare for the grand opening on Monday and his customer was satisfied.
~Brian, Stripe It Right
Working with Stripe It Right, and offering solutions is what we do at PaladinID…it’s why we come to work every day. Thank you, Brian, for allowing us to serve you and contributing to this successful Stripe It Right warehouse installation. We look forward to our next project together…perhaps with a little more lead time!
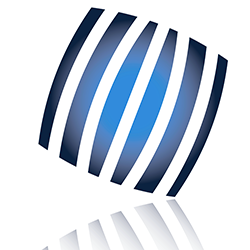
Got Labeling Questions? Our AI Assistant Has Answers - Chat Now!
For more information on PaladinID
Get Help With Your Next Label Project
We have over 35 years of providing exceptional service and labeling products to the world. Take the first step to an easy, stress-free solution for your label needs by contacting us.
Schedule a call below or email [email protected]
Make Your Mark
“Making companies more competitive by offering the correct label printing solution, on time, within budget, while creating unmatched value”.
About PaladinID, LLC
PaladinID develops and supports high-performance barcode labeling applications. We work with our clients to “Make Your Mark” by providing the expertise and tools necessary to create an entire product label printing solution. Located in central New Hampshire, PaladinID has been serving Massachusetts, Vermont, Maine, Connecticut, Rhode Island, New England, and beyond for over 30 years, and in 2017, became an RFID-certified company. We look forward to working with you.
You may be interested in our other services:
Product Labels
Product Labels
Labels for every type of application: Blank, Pre-printed, Variable data
Label Printers
Label Printers
We sell and support: Direct/thermal transfer, Inkjet, Laser
Printer Ribbons
Printer Ribbons
We sell ribbons for ALL barcode printers including: Zebra, Datamax, Sato, Intermec
Flexible Packaging
Flexible Packaging
We offer a wide variety of packaging containers for your products.
Label Software
Label Software
Software for all barcode printing and product labeling.
Label applicators
Label Applicators
Wide selection of applicators: Desktop/Mobile, Applicator only, Print & apply